Scopri i vantaggi della macinazione criogenica per il riciclo di pneumatici e gomma
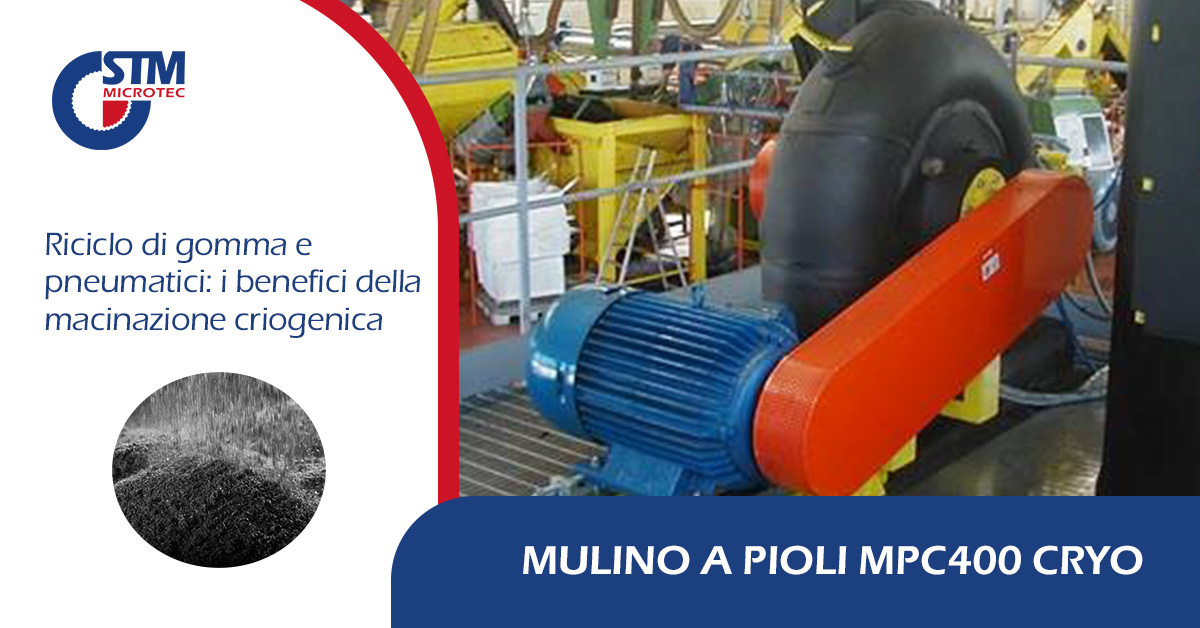
Negli ultimi anni, sempre più aziende si sono orientate verso un modello di business eco-sostenibile. Un settore emerso in questo campo è quello del riciclo degli pneumatici usati e usurati, in seguito anche a normative comunitarie di riciclo e recupero di materiali a fine vita.
A livello industriale i processi di polverizzazione che tradizionalmente vengono eseguiti a temperatura ambiente possono essere condotti a temperature criogeniche con l’obiettivo di ottenere una miglior qualità del prodotto macinato ed una riduzione dei consumi energetici.
Questo è possibile perché prodotti come lo pneumatico, che presentano bassi punti di rammollimento, elasticità e hanno caratteristiche di termosensibilità come gli elastomeri, vengono efficientemente polverizzati portandoli, con l’impiego di azoto liquido, alla loro temperatura di infragilimento.
La criomacinazione viene impiegata con successo nei processi di macinazione di scarti di gomme, di elastomeri e in tutti quei settori dove la criogenia rende più efficiente la tecnologia di macinazione utilizzata, senza danni alla struttura fisico chimica o reticolare del prodotto finito.
Applicazione Criogenica – Azoto Liquido
L’azoto liquido svolge principalmente tre funzioni: raffredda rapidamente il materiale alla temperatura di infragilimento prima che entri nel mulino di macinazione. Mantiene costante la temperatura di lavorazione, assorbendo calore sviluppato durante l’operazione di macinazione.
Le sostanze criomacinate presentano caratteristiche fisiche diverse da quelle ottenute con i tradizionali processi di macinazione, proprio per il modo in cui viene rotta la struttura del materiale.
Ecco le principali differenze tra i due processi:
CRIOGENIA
- La gomma da pneumatico infragilita criogenicamente produce grani omogenei, a forma cristallina, cubica;
- Miglior resa produttiva
- Miglior qualità finale del prodotto, senza sfibramenti o rotture
- Riduzione del consumo di energia
- Incremento di qualità del prodotto finito
- Minor scarti di lavorazione (per surriscaldamento)
- Maggiore finezza ed omogeneità del prodotto
- Riduzione della quantità di materiale da riprocessare
TEMPERATURA AMBIENTE
- Lacerazioni nella matrice iniziale a causa della scorrevolezza dei piani cristallini o delle particolari strutture reticolari,
- Polveri con caratteristiche fisiche non uniformi.
- Alto consumo energetico dovuto alla bassa produttività oraria
- Possibilità di fusione del materiale sui rotori di macinazione
- Bassa quantità di particolato fine
- Alto riciclo dei materiali sopra vaglio.
Ma quali sono le parti più rilevanti di questo processo? Vediamo come lavorano e a cosa servono le principali soluzioni coinvolte.
Tramoggia di ricevimento in quota e dosatore integrati alla struttura
Tutto il sistema è concepito per contenere e utilizzare la criogenia solo in un punto specifico dell’impianto, le altre zone, la tramoggia di contenimento, come quella di dosaggio, invece lavorano a temperatura ambiente.
Il controllo viene effettuato tramite sensori, valvole e metal detector per la corretta sorveglianza del materiale.
Metal detector
Il polverino da pneumatico contiene per sua natura varie contaminazioni metalliche, un buon sistema di defezione, sia semplice che più avanzato, è necessario per la conservazione degli organi di macinazione.
Valvola proporzionale Azoto Liquido
Controlla tramite regolazione PID elettroniche del quantitativo del liquido da iniettare nel circuito, lavorando in sincronicità al recupero dei gas freddi e della temperatura di lavoro della camera di macinazione.
Girante Contro rotante a Pioli in fusione speciale
Giranti di macinazione ad alta efficienza di macinazione, con dischi antiusura e pioli a forma cilindrica in fusione, studiati appositamente per polimeri altamente abrasivi.
Facilità di accesso alla camera di macinazione e semplice sostituzione dei pin e delle parti di usura, grazie alla costruzione a dischi accoppiati sono i punti di forza di questa soluzione.
L’azoto, collegato tramite tubazione flessibile alla coclea criogenica, viene nebulizzato tramite ugelli sulla gomma.
La temperatura di lavoro controllata garantisce la massima efficienza del sistema, la posizione in quota senza movimentazione a tubazioni del prodotto, la forma contenuta nel guscio di armaflex, permette di mantenere le frigorie di esercizio e sfruttare al meglio le energie di lavorazione.
Dati in campo: MPC 400 – CUNEO
Il mulino a pioli controrotanti MPC400 Contraplex ha una produttività di polverino di pneumatico di circa 500 kg/h ad una granulometria di 100%<500µm
La temperatura di lavoro ideale è di circa – 28°C e le condizioni di isolamento termico, nonché la possibilità di riciclo dei gas freddi non esausti, permettono di avere un consumo gestione contenuto
Questo mulino è stato integrato alla linea di produzione del cliente, il prodotto vagliato è stato poi posto nei big bag. Il sopra vaglio > 500µm è esiguo e vi così un riciclo di basse quantità che non e variano la produttività del materiale grezzo.
In conclusione, dopo la fase di raccolta e triturazione a blocchetti e la macinazione a grani di 5mm con eliminazione del 99% di fibre tessili e fibre metalliche grazie all’impianto STM Microtec è stata ottenuta una Criomacinazione al 100% <500 µm.